Industrial gaskets
Industrial gaskets is a generic term for seals for use in static, industrial applications. Industrial gaskets are known under different names such as flange gaskets, flat gaskets, machine gaskets, rubber gaskets, steel gaskets, rubber-steel gaskets, etc.
What is a gasket?
A gasket is a material or combination of materials specifically designed to be fitted between two flanges to create a tightness that must be maintained:
- Prevent leakage of a medium between the packed surfaces
- Prevent the ingress of dust, dirt, liquid and other contaminants
- Maintain pressure or negative pressure in the space being packed
- Ensure a combination of the above features
Standard packs and unique custom solutions
Betech offers industrial gaskets according to international norms and standards, often used in repair and maintenance applications but also in new constructions and plants.
In addition to standardized solutions, Betech develops gaskets and seals according to unique customer specifications and material combinations.
Specification and design is often done in close collaboration with machine builders and OEM industries with the aim of optimizing the entire application and thus product quality, lifetime and competitiveness.
Advice on optimal seals
Betech is not just a distributor or manufacturer of gaskets, but your partner that adds value to the entire value chain from the development phase, in the supply and production line and through the service period.
the development phase
During the development phase, our team of experienced consultants and product experts assist in optimizing material selection, product design and manufacturing methods. Single prototypes are quickly produced for development and testing.
Supply and production
In the supply and production line, our broad product portfolio and versatile production facilities allow you to gather all purchases in one place.
Service period
Manufacture of flat gaskets
Gaskets with self-adhesive coating
Do not use masking tape, duct tape or other devices to secure the gasket during installation. Betech can offer to apply various self-adhesive materials to the back of the gasket to ensure a uniform surface and sufficient fixation on the actual gasket surface.
Large packs are cut into segments
Gaskets whose dimensions exceed the dimensions of the material used for that application are produced in segments that are either glued together, vulcanized or produced by dovetail jointing. For graphite materials, the dovetail joints can be reinforced using graphite tape. If the material is FJ2815, a paste is used to increase the density of the joint.
Key factors when choosing a gasket
In the following you will be introduced to the most important technical aspects of industrial gaskets. We also have some practical tips for handling and installing flange and flat gaskets, among other things.
The most important requirements for the package or packaging material include:
- density
- lifespan
- disassembly
- thermal conductivity
- elasticity
Below you can read about how these factors influence the choice of packaging material.
Density - pressure, temperature and media
Every gasket needs to provide some form of sealing, but the operating conditions under which the gasket must work can vary greatly and inherently determines the choice of gasket type and material.
Most importantly, the gasket must be able to withstand a given Pressure and a certain temperature in addition to the impact of one or more Media such as superheated steam, combustion gas from engines, air, oil, chemicals, etc.
You must ensure that the gasket can withstand the mechanical stresses it will be exposed to - especially the pressure it will be sealed against.
In addition, the gasket must be able to withstand the chemical influences it is exposed to so that it does not corrode or dissolve. And it must be able to withstand the temperature, high and low, during operation and peak loads.
As different gasket materials withstand different maximum surface pressures, pay attention to the ratio between the loaded part of the gasket and the thickness of the material.
If the gasket is to be used in glands, the gasket may twist, which must also be taken into account when choosing the material.
When designing and dimensioning a joint, the lines of force in the structure must be taken into account to ensure the most optimal joint possible.
Before you choose a gasket material, you need to know what mechanical, chemical and temperature influences the material must be able to withstand.
Lifetime
You can only expect the gasket to last a long time if you have used a material that is suitable for the purpose.
It is important that a gasket material does not change properties during use. If you choose an unsuitable gasket material, the gasket may lose its elasticity over time, you may risk the gasket becoming brittle or dissolving.
Today, technology has advanced to the point where you can count on a properly selected gasket to last as long as the machine parts it seals between.
Separation
It is often important that the connection that has been sealed can be separated again - meaning that the seal can be removed without damaging the sealed surfaces. Most gasket materials have a standard anti-stick-Silicone surface treatment, which in some cases can be replaced by a graphite or PTFE treatment - on one or both sides.
Thermal conductivity
When choosing a gasket material, you sometimes need to consider whether the gasket will also act as a heat conductor or if it will act as a thermal insulator, as gasket materials have very different thermal and electrical properties. The consequences of choosing the wrong material or the wrong type of gasket can be disastrous - both in terms of function, safety and the environment.
Elasticity
The elastic properties of the gasket material also play a role in its use. In order for the material to maintain the tightness of the joint during its expected lifetime, it must be able to compensate for any small flange misalignments and surface roughness. Compensation for such non-uniformities is achieved through the surface pressure applied to the material and its elastic properties.
Three main categories of gaskets
Gaskets can be divided into three main groups: non-metallic gaskets, semi-metallic gaskets and metal gaskets.
Non-metallic gaskets
Rubber - Cork - Fiber - Laminates - Plastic
Non-metallic gasket materials can be made from different types of rubber materials, rubber cork, different fiber systems, gasket laminates or PTFE materials in sheet format.
- Rubber sheets are manufactured in the traditional rubber types NBR, HNBR, EPDM, CR, NR, VMQ and FPM.
- Rubber cork is made from cork granules of different sizes bonded with a polymer such as NBR, CR, EPDM or VMQ.
- A fiber system can consist of cellulose fibers, aramid fibers, a combination of glass and aramid, carbon fibers or vermiculite with various fillers added and bonded with rubber or other polymer.
- Gasket laminates consist of a stainless steel core coated with a gasket material on both sides to increase the tensile strength of the material. The facing material is typically graphite, mica or vermiculite.
- PTFE materials range from so-called virgin PTFE to expanded PTFE in mono- or multi-oriented grades.
Sheet materials are usually used in applications with Low to medium pressure, general media, extreme chemicals and high temperatures.
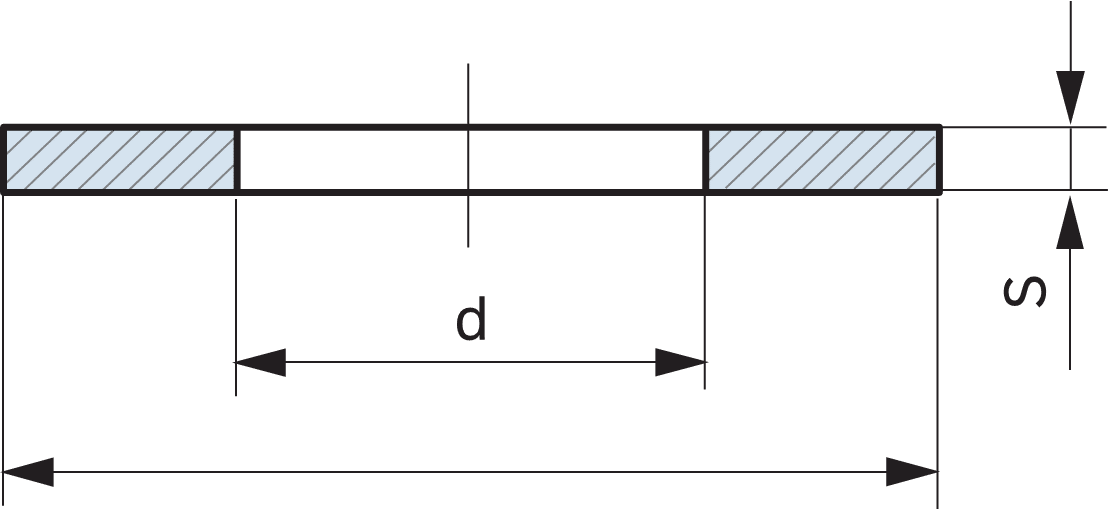
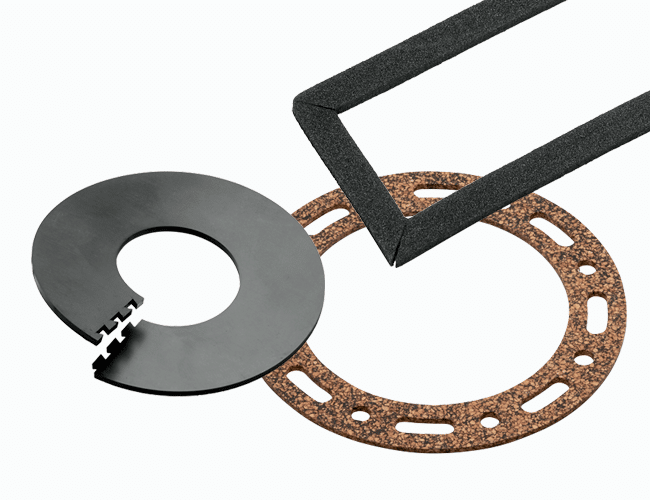
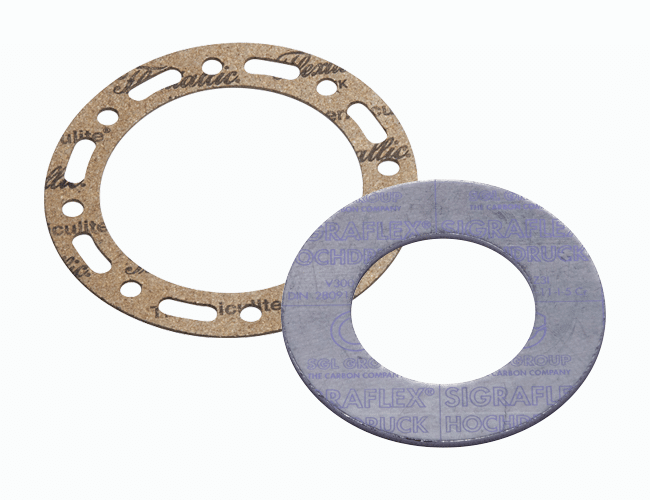
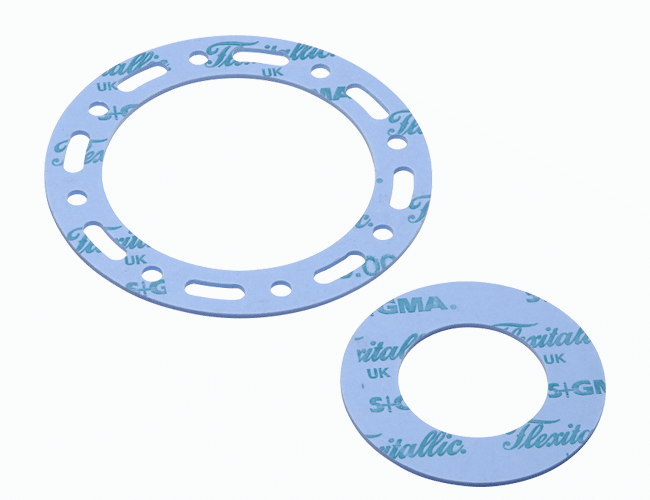
sEMI metallic gaskets
Semi-metallic gaskets consist of a metal material bonded with either graphite, PTFE or vermiculite. Semi-metallic gaskets can be spiral wound gaskets (SWG), cam profiled gaskets or Metal Re-inforced Gaskets (MRG).
In semi-metal gaskets, the metal part provides the strength, while the facing material creates the seal. These gaskets are used in low to high pressure applications. How high temperatures they can withstand depends on the steel grade and facing material.
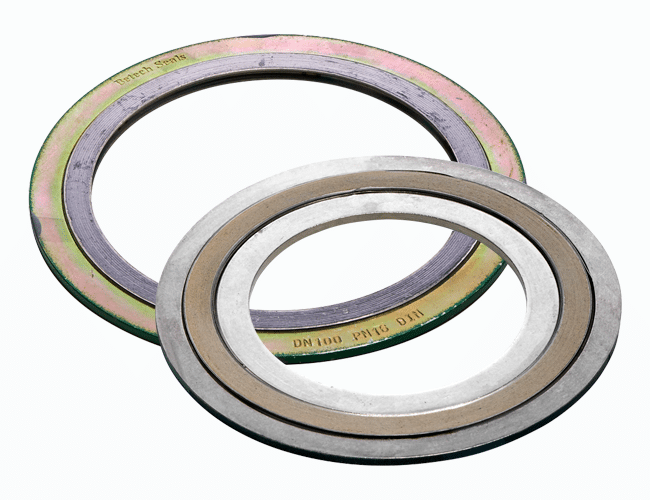
SWG
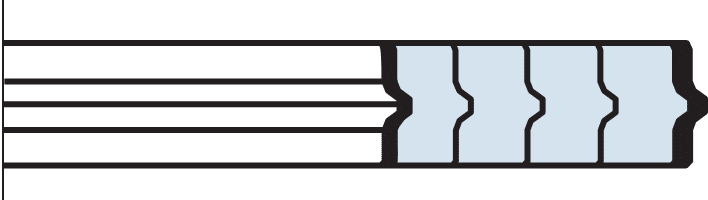
Kammprofile
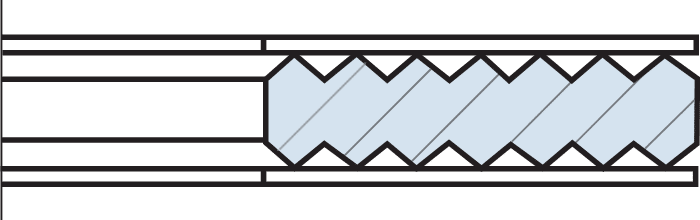
The kammprofile gaskets consist of a milled metal core that is coated with graphite, PTFE or vermiculite as a sealing element.
MRG
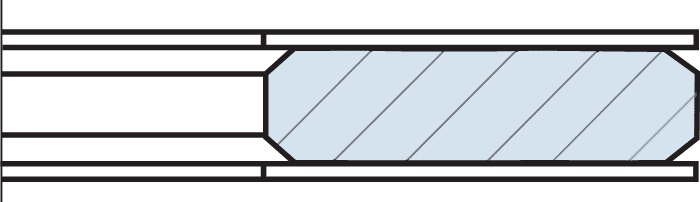
MRG gaskets consist of a steel core coated with graphite or PTFE as a sealing element.
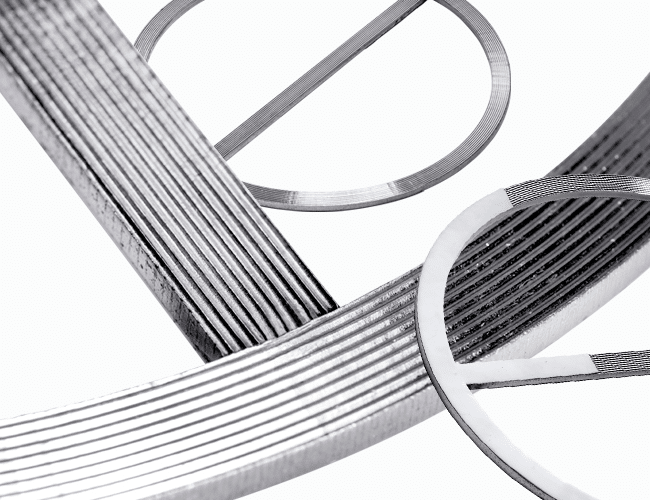
metal gaskets
Metal gaskets can be manufactured in a myriad of shapes and sizes as well as different metal alloys and Primarily used in high pressure and high temperature applications. Metal gaskets require a high surface pressure to deform the gasket in the flange joint.
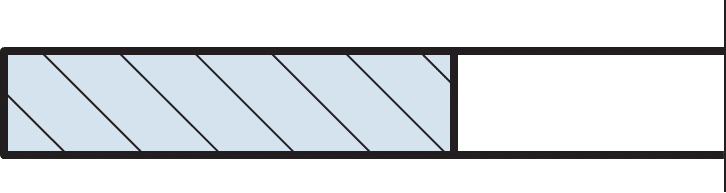
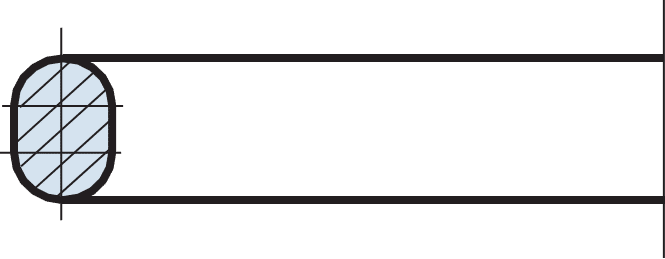
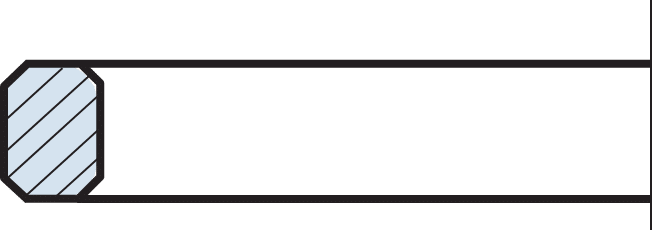
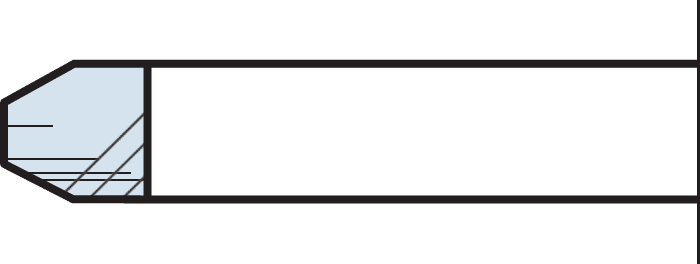
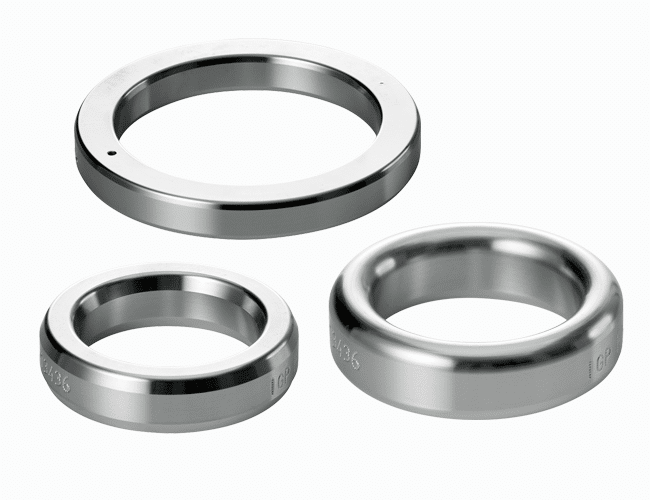
Flat metal gasket
Metal gasket, oval
Metal gasket, octogal
Metal gasket, trapezoid
Avoid mistakes and get the best results with your gaskets
With good preparation, proper storage and installation, you ensure that the gasket and the entire sealing system meet the requirements and properties needed for safe operation and longevity of the application.
How to prepare for installing the gasket
Correct installation of a gasket is a prerequisite for a reliable flange connection. But also bolts and the surfaces to be gasketed must conform to the surface pressure required for the selected gasket material or gasket.
Clean the seal faces carefully without scratching them and make sure the seal face is dry. Check bolts, nuts and washers for defects and rust. Clean or replace if necessary.
Bolts, nuts and washers should be lubricated on all pressure-transmitting surfaces.
Check that the gasket has the correct shape and is made of the correct material, and that the material is free of defects and scratches. Always use dry gaskets.
How to install the gasket correctly
Place the gasket carefully between the flanges. Never use wax ointment, abrasives, grease, etc. on the gasket or flanges. If you need to secure the gasket to the flange, consider a gasket with adhesive on the back.
Bring the flanges together and tighten the bolts by hand. For large flanges, a wrench can be used. Always use the correct tool, i.e. calibrated torque wrench or other controlled tightening tool.
To achieve an even distribution of surface pressure, cross-tighten the bolts to the recommended surface pressure in 5 steps:
- Tighten the bolts by hand.
- Tighten to approximately 30 % of recommended torque.
- Tighten to approximately 60 % of recommended torque.
- Tighten with 100 % of recommended torque.
- Retighten with 100 % torque clockwise to get a uniform surface pressure.
For safety reasons, you should never recycle used gaskets.
Download brochures and guides
Choice of gaskets
26-page guide to gasket technology, critical factors of the sealing system, gasket types, material selection and gasket handling (Danish or English)
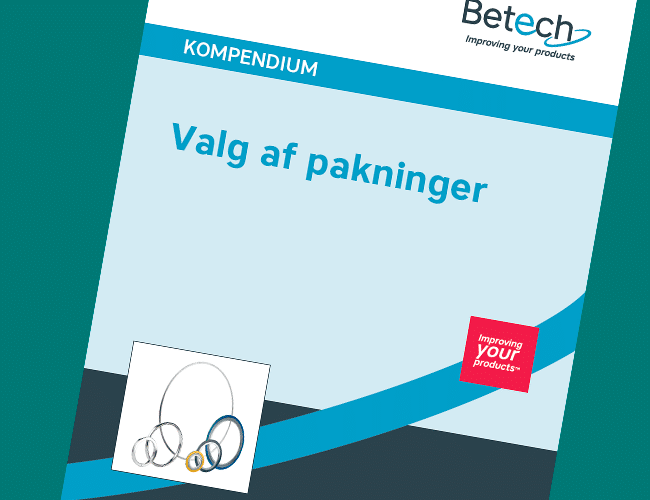
Rubber - generic properties
This handy overview gives you a quick overview of the temperature range, resistance and physical properties of the most common types of rubber and silicone.
Download the table so you have it at hand the next time you need to track down the right choice of technical rubber. (Danish and English)

Installation of gaskets
Handy guide to good preparation, handling, assembly and tensioning of industrial gaskets (Danish)
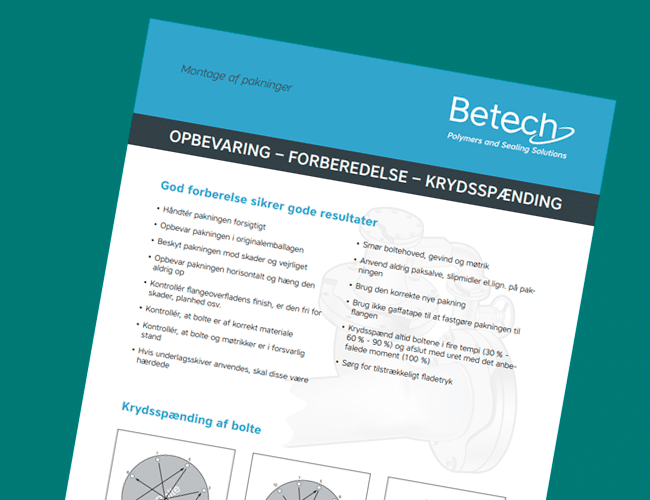
* When you download brochures, catalogs and the like, you agree that Betech can contact you.
Concepts, definitions and norms
Static vs. dynamic seals
A seal is basically a device designed to close (seal) an opening or make a joint tight against a liquid or gaseous medium. There are two main principles: static and dynamic seals.
Static seals
With static seals, the seal is between two surfaces that do not move relative to each other (a static application). In static applications, it is the surface pressure that creates the seal.
Dynamics seals
With dynamic seals, the sealing occurs between two surfaces that have a relative movement (dynamic application), e.g. a rotational movement of a shaft in relation to the housing or a piston movement of a rod or piston in a cylinder. However, some seal types that are designed for dynamic applications are also used in static applications.
In dynamic applications, media pressure helps create density. To learn more about application and installation, please refer to our O-ring product catalog.
International norms and standards
Betech supplies industrial gaskets - flange gaskets and cut flat gaskets - according to the following norms and standards:
ASME B16.20 and ASME B16.21 - pressure, dimensioning, tolerances, etc. for pipes, flanges, valves and gaskets
BS3381 - specifications for spiral wound gaskets
API 6A - equipment specification for oil/gas applications
API 6FB - Testing pressure tightness under fire
API 607 - Fire test for valves
EN 12560-6 - Flange joints with comb profile gaskets
EN 1514-1 - flange assemblies with non-metallic gaskets.
EN 1514-2 - dimensioning etc. of spiral wound gaskets
EN 1514-6 - dimensioning etc. of coated comb profile gaskets
Gasket thickness
The gasket should always be chosen as thin as possible for maximum strength and minimal leakage through the gasket material.
Thickness of the gasket material is related to the following parameters:
- Surface roughness: a small Ra value results in a thinner gasket.
- Compressibility: low compressibility of the material results in a thicker gasket.
- Surface pressure: a high surface pressure results in a thinner gasket.
fLOAD PRESSURE
If a gasket material is exposed to too much surface pressure, the material will creep a lot. This changes the elasticity of the material so that it is unable to compensate for changes in surface pressure.
Maximum allowable surface pressure
For a specific gasket material, there will always be a specific maximum allowable surface pressure in relation to temperature and material thickness. A thin gasket material will always be able to withstand a higher surface pressure than a thick material. The thinner the material, the greater the demands on the parallelism and roughness of the flange joint.
Postponement (Blow Out)
If the gasket material is soft, there must also be sufficient friction under pressure between the gasket material and the flange to prevent gasket ejection from the joint, also known as a blow out.
(Hydrostatic End Force)
If a joint is subjected to internal pressure, the pressure will try to separate the parts of the joint, causing the surface pressure to drop on the material. This internal pressure must therefore be taken into account, also known as hydrostatic end forcewhen calculating minimum operating surface pressure and test pressure, which in most cases will be much higher than the operating surface pressure.
Tightening and lubricating - torque and friction
To ensure correct surface pressure, bolts should be tightened with a torque wrench. In addition, bolts, nuts and washers should be lubricated to minimize friction and increase the pre-tensioning force of the bolts. Assume a friction of 0.14 for lubricated joints and 0.3 for unlubricated joints.
Gasket types and surface pressure
The materials listed below are normally used in the specified ranges, but when installing, media pressure, gasket thickness and temperature must also be taken into account.
Material type
- Rubber cork
- Rubber materials
- Cellulose materials
- Fiber-based materials
- Graphite laminates / vermiculite
- Graphite high pressure
- PTFE sheet materials
- SWG, graphite / PTFE / vermiculite
- SWG IR
- Kammprofile gaskets, graphite / PTFE
- MRG gaskets, graphite
- Metal gaskets RTJ, soft iron
- RTJ AISIi
- RTJ F 5
Min.
- 2 MPa
- 2 MPa
- 5 MPa
- 20-30 MPa
- 20 MPa
- 30 MPa
- 13 MPa
- 50 MPa
- 50 MPa
- 20 MPa
- 20 MPa
- 235 MPa
- 335 MPa
- 400 MPa
Max.
- 7 MPa
- 10 MPa
- 70 MPa
- 80-180 MPa
- 110-160 MPa
- 500 MPa
- 195 MPa
- 150 MPa
- 300 MPa
- 500 MPa
- 110 MPa
- 525 MPa
- 750 MPa
- 900 MPa
We are ready to help you
The products and information on these pages are examples from our almost limitless universe of possible product solutions.
If you didn't find what you were looking for, we are ready to help you find the right solution.